Installing a metal shingle roof on a residential home will cost, on average, between $11.50 and $19.50 per sq. ft. In this buying guide, we’ll explain all the important factors that determine the total cost of a metal shingles, along with pros and cons. We’ll also cover material costs of various metal shingle options and draw some comparisons to other popular roofing materials.
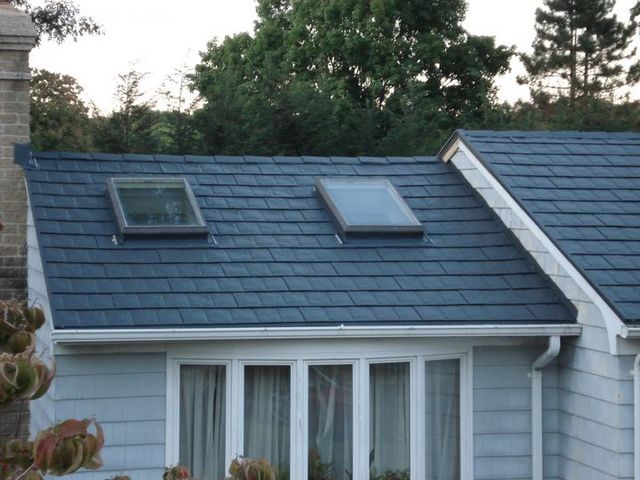
It’s perhaps most important to realize that of the three primary options for metal roofing (the others being Standing Seam at the high-end, and Corrugated and Ribbed Metal Panels at the low-end), metal shingles and tiles are in the middle of the pack in terms of costs.
Understanding Your Options
At first mention, metal shingles sound bland or traditional, or perhaps too risky of an option for an HOA or in an area where metal would clearly be outside the norm (i.e., all your neighbors have asphalt roofs).
Yet, when researching metal shingles styles and options for residential homes, you might be surprised to pull up some images that look a lot like asphalt shingles. 😉
Why would that be? Because the reality of metal shingles today, is that these are really metal tiles that are intended to mimic just about all other possible roofing styles designed for sloped roofs; slate tiles, ceramic tiles, asphalt shingles, cedar shakes and say redwood shingle are all materials that metal shingles can mimic.
From the curbside view, it would be hard to tell the difference between the metal material and its usual counterparts. That’s how diverse the metal roofing industry has gotten.
Add to this the idea that metal itself can have a pleasing appearance, as is the case with copper, zinc, painted aluminum and steel tiles. Gone are the days when metal shingles would only have a silver/gray, metallic appearance.
Key Fact: There are really two basic types of metal shingles, or metal tiles: G-90 galvanized steel coated with a protective layer of zinc plating, often finished in a factory-applied Kynar 500 paint finish, and the second type finished with stone granules referred to as stone-coated steel tiles.
Did you know? The “G-90” refers to the amount of protective zinc plating, as in .90oz per square foot of steel sheet.
Read more